Zip Pack
Zip Pack is biodegradable packaging made for delivering emergency healthcare for all. The use of innovation and research in alternative materials can further a forward-thinking, eco-conscious, and responsible approach for a more sustainable healthcare industry.
Time Frame
4 Weeks– 2022
Team: Individual project
Under the guidance of Max Pratt
Skills: Material Research, Market Trend Research, Physical Prototyping, Testing
How might we reduce plastic in the healthcare industry?
By minimizing plastic usage in medical devices and packaging, healthcare organizations can contribute to a significant reduction in environmental pollution, conserve resources, and decrease the risk of chemical exposure and microplastic contamination.
Zipline
Zipline is an emerging healthcare provider by manufacturing and operating delivery drones. Their goal is to deliver blood, healthcare equipment, and food to medical sites and homes who struggle to get access to emergent care.
PROBLEM STATEMENT
When drone packages are delivered to homes and during emergencies, the likelihood of the plastic or foam packaging being properly recycled or disposed is low.
DESIGN GOALS FOR AN ALTERNATIVE PACKAGING MATERIAL
Low-Energy -Manufacturing
Plastic and foam are considered to have energy-intensive processes.
Biodegradable
To complete a circular system when the package is disposed, I set a key goal as the biodegradability of the material.
Lightweight and Durable
Delivering packages using drones has
Mycelium is a type of fungi or mushroom that is grown from agricultural by-products (hemp.)
Comparative Analysis of Packaging
I compared mycelium with the traditional packaging: cardboard, plastic, and foam.
Although cardboard and plastic is more affordable, mycelium proves to have the lowest carbon footprint due to the low energy manufacturing process compared to plastic and foam.
(Ecovative Design) (Supplychain.org)
Observe
After experimenting, researching, and interviewing experts at the Nature Lab, I considered various biomaterials such as Kombucha leather, cellulose, biofoam, dehydrated food waste, and more.
I chose mycelium as the most viable option out of biodegradable materials due to its favorable qualities: waterproof, thermal insulation, biodegradable, medium long lifespan (6weeks-10 years), and a low-energy manufacturing process.
SKETCHING–
A functional and simple shape was necessary for the feasibility for mass manufacturing for mycelium to grow in a set mold.
MOODBOARD–
Warranted, smart-design, and an uplifting material.

1. Activating hemp waste substrate using flour and water
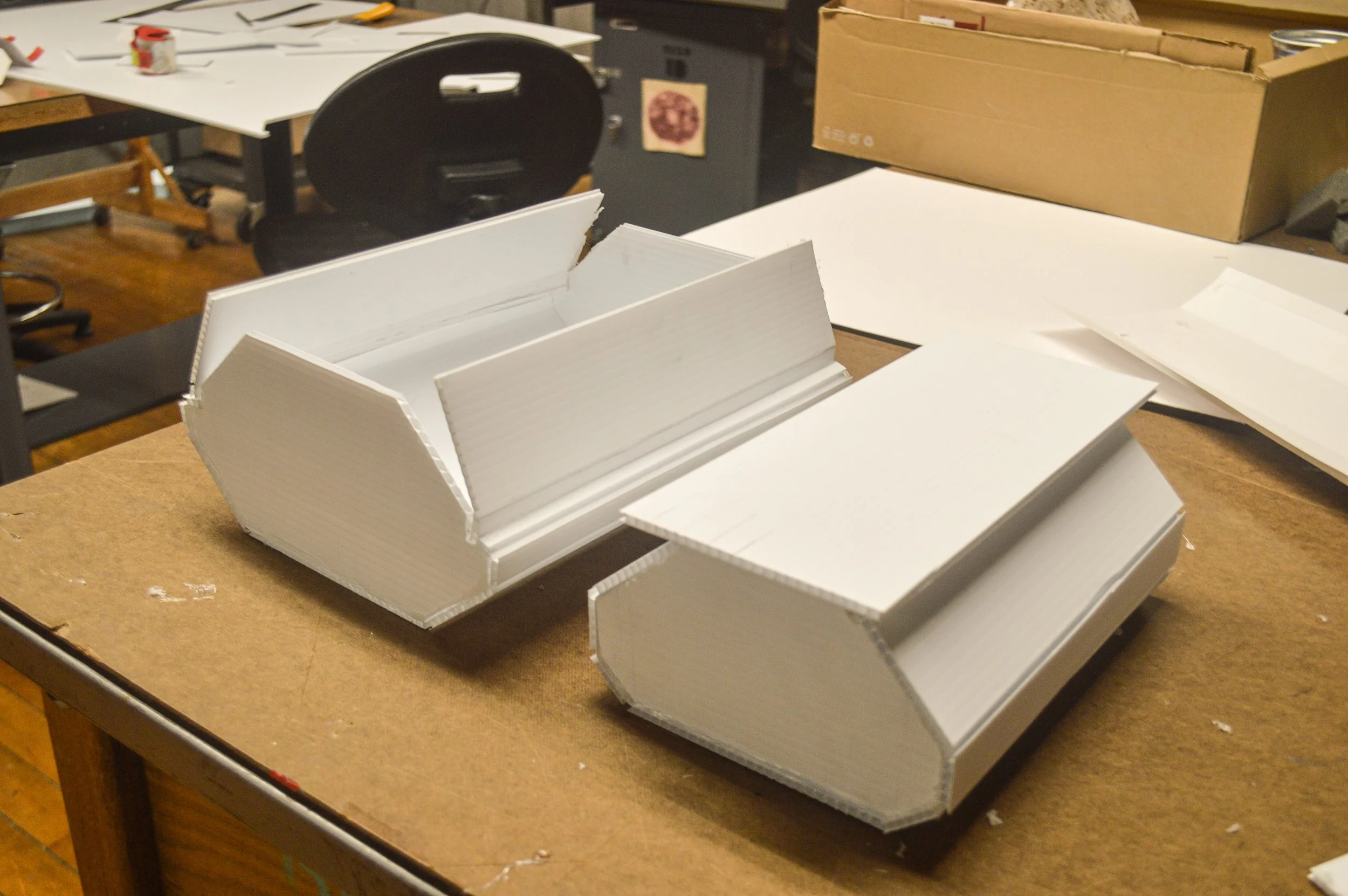
2. Creating the mold for mycelium to grow into
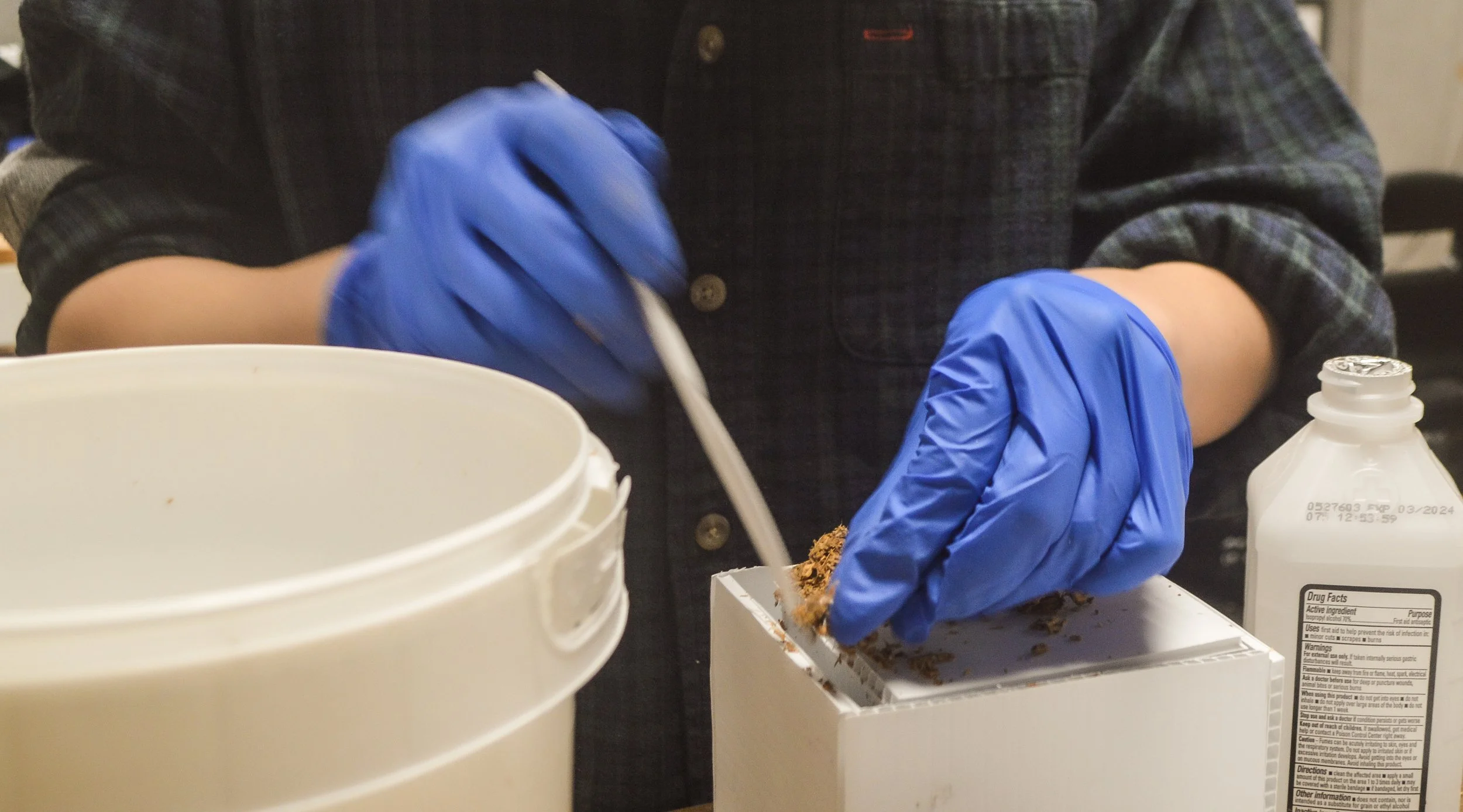
3. Filling the mold with hemp substrate
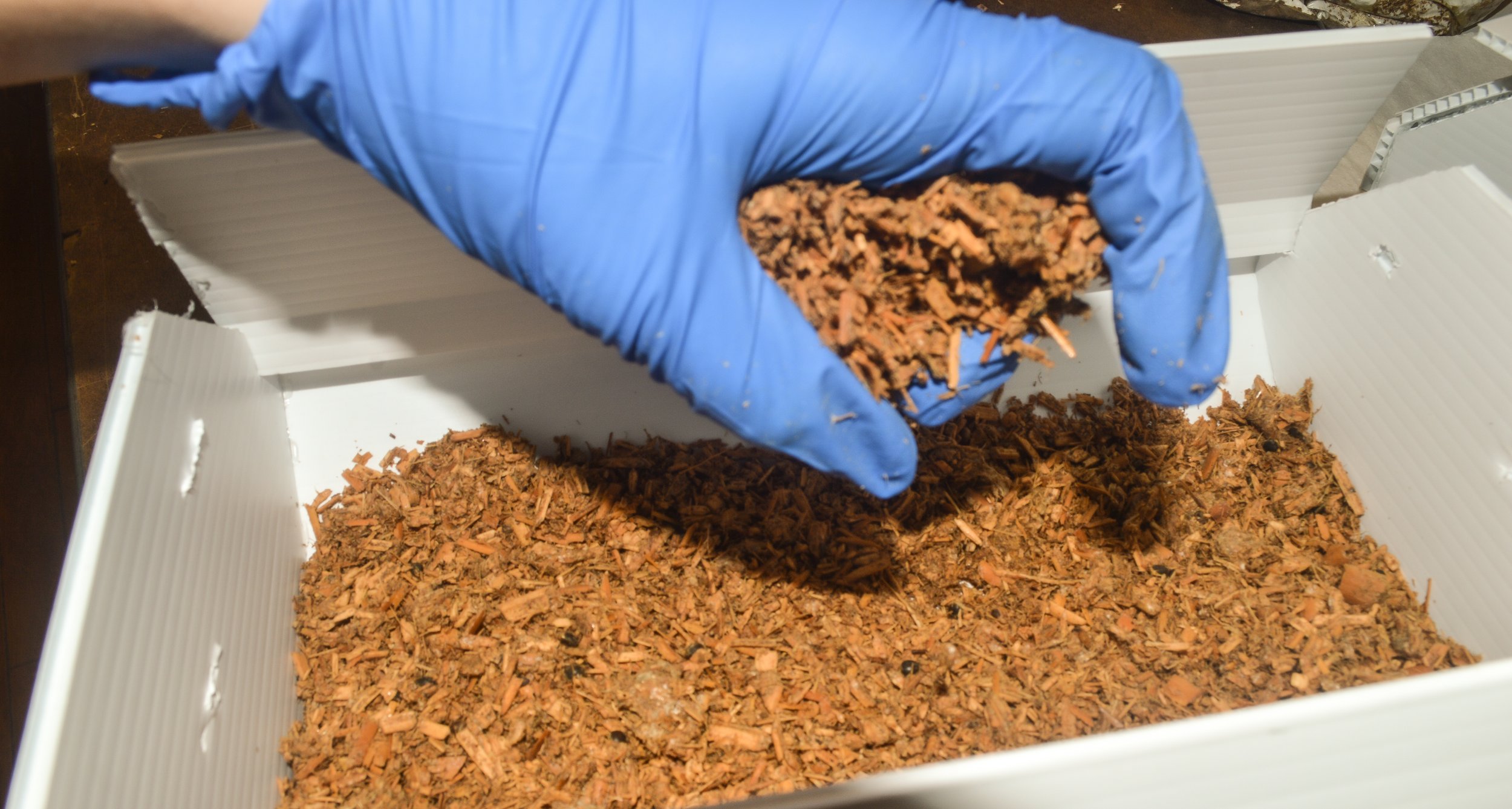
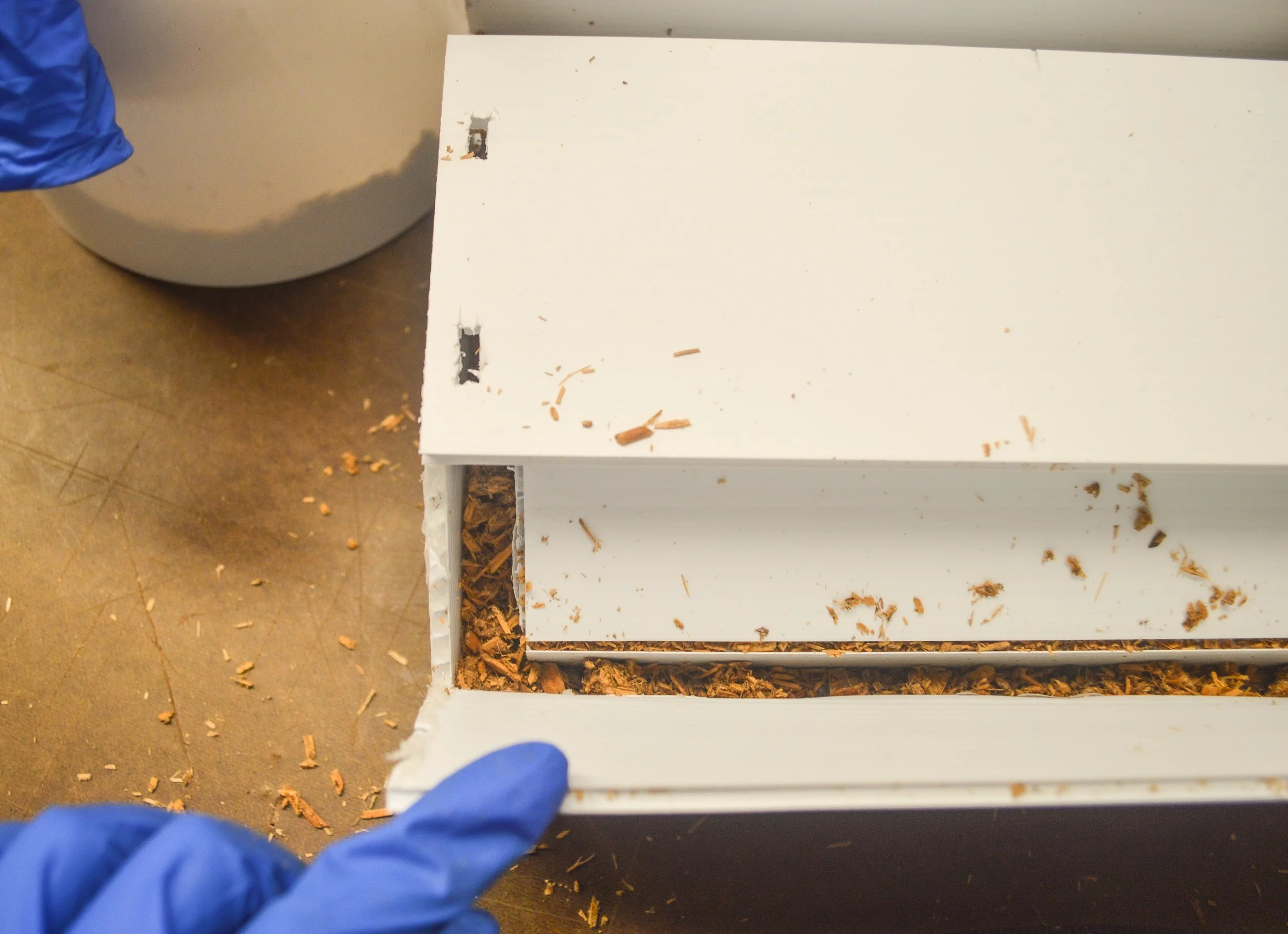

4. After 8 days, the mycelium has grown to fill up the mold structure, resulting in a hollow shell.

Proof of Concept Testing– Egg Drop
This rudimentary test was executed to prove the lightweight and durable qualities of mycelium as packaging. Two eggs weighing around 4 ounces, were dropped from a range of 6ft to 12ft.
Out of 25 egg drops, only two eggs resulted with slight fractures of the shell. Although this test was basic, it helped me confidently proceed with my choice of using mycelium.